NEU!! Entwickelt SxMDs mit einem strukturierten eQMS, einschließlich auditfähriger SxMD-Vorlagen, die an EU- und US-Standards angepasst sind. Mehr Erfahren!
GUDID Must Knows: The FDA Global Unique Device Identification Database
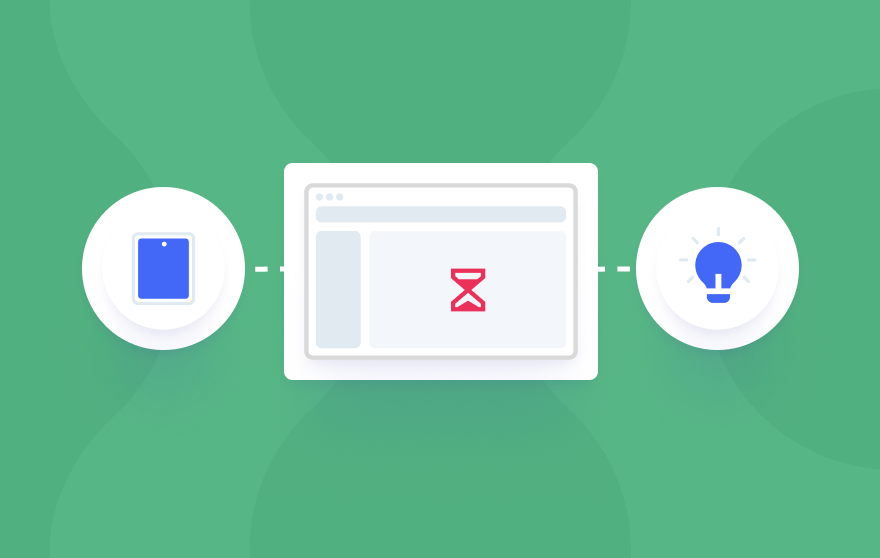
The FDA's Global Unique Device Identification Database (GUDID) is now fully operational, marking a significant milestone in medical device regulation. For medical device manufacturers gearing up to submit their data to GUDID for the first time, understanding the requirements is very important.
In this comprehensive guide, we'll delve into the intricacies of GUDID, providing a thorough understanding of its significance, operation, and submission process.
What is GUDID?
GUDID, short for Global Unique Device Identification Database, serves as a digital repository established by the FDA to store detailed information on all medical devices bearing a unique device identifier (UDI). It acts as a centralized hub for critical device specifications, including manufacturer details, intended use, safety, and handling requirements.
Introduced in 2013 as part of the FDA's UDI Final Rule, GUDID plays a pivotal role in the UDI system, ensuring comprehensive device traceability and facilitating post-market surveillance.
Understanding UDI
At the heart of GUDID are Unique Device Identifiers (UDIs), distinct codes used to identify medical devices throughout healthcare supply chains. UDIs consist of two primary elements:
Device Identifier (DI): This component identifies the manufacturer and the specific model or version of the device.
Production Identifier (PI): Comprising variable characteristics such as manufacturing date, expiration date, lot number, or serial number, the PI provides additional details about the device.
Combining the DI and PI forms the complete UDI, essential for accurate device identification and tracking.
Submission Requirements
Device labelers, as defined by FDA regulations, bear the responsibility for GUDID submissions and general UDI compliance. While the labeler is typically the device manufacturer, other entities such as specification developers, reprocessors, assemblers, or relabelers may also fulfill this role.
GUDID mandates the submission of specific data attributes, totaling 57 in all. These encompass various categories such as device identifier information, commercial distribution, alternative identifiers, customer contact details, manufacturing information, device dimensions, storage and handling instructions, and sterilization specifications.
Preparing a GUDID Submission
Effective preparation is key to a successful GUDID submission. Manufacturers must ensure adherence to Standard Operating Procedures (SOPs) for organizing, collecting, and validating data, laying the foundation for accurate submissions.
Two submission methods are available:
Structured Input: Ideal for low-volume submitters, this method involves manual data entry via the GUDID web interface.
HL7 Structured Product Labeling (SPL): Intended for high-volume submitters, this approach utilizes the FDA Electronic Submissions Gateway (ESG) for submission via XML files.
Additionally, manufacturers must understand the roles associated with GUDID submissions, including Regulatory Contacts, Labelers, and Coordinators, as outlined by FDA guidelines. Obtaining a Data Universal Numbering System (DUNS) number and certification is mandatory for UDI labelers. Learn more about launching a Medical Device in the US vs the EU and the key differences here in our latest video. In addition you can learn about FDA 510(k) submissions here.
GUDID represents a monumental advancement in medical device regulation, promoting enhanced device traceability, patient safety, and post-market surveillance. By comprehensively understanding GUDID requirements and diligently preparing data submissions, manufacturers can navigate the regulatory landscape with confidence, ensuring compliance and contributing to the advancement of healthcare quality and safety.
For further insights into FDA regulations and compliance, explore these additional resources:
Navigating the FDA 510(k) Submission: Complete Guide
Discover step-by-step guidance for navigating the FDA 510(k) submission process from start to finish.What is the QMSR FDA Alignment with ISO 13485
Learn about the alignment between Quality Management System Regulation (QMSR) and FDA requirements through ISO 13485.How to Unlock FDA eSTAR to Help Streamline Approvals
Explore strategies and tips for unlocking the potential of FDA eSTAR to streamline the approval process effectively.How to Manage SAMD Technical Files with the FDA
Gain insights into managing Software as a Medical Device (SAMD) technical files in compliance with FDA regulations.
For companies looking to accelerate development of their innovative medical device technologies, the Matrix Requirement platform is an easy-to-use, flexible, all-in-one software solution that: facilitates collaboration of employees on design control, and quality management to streamline medical device design, establish lean quality management, accelerate product certification and go-to-market, and maintain regulatory compliance.
Take a spin of Matrix Requirements QMS and ALM to see how these features work alongside your GUDID application & discover how they can improve your day-to-day operations. If you want to get a deeper understanding, schedule a demo and take the first step toward a more efficient, user-friendly, and secure solution.