NEU!! Entwickelt SxMDs mit einem strukturierten eQMS, einschließlich auditfähriger SxMD-Vorlagen, die an EU- und US-Standards angepasst sind. Mehr Erfahren!
Quality Assurance vs. Quality Control : The must know differences
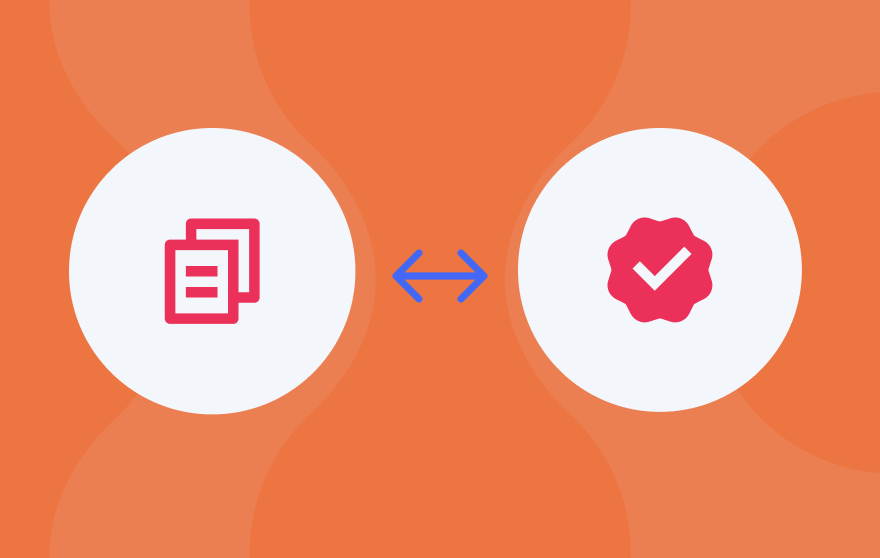
Quality is a fundamental aspect across various industries, including medical devices, where safety and performance are paramount. Ensuring products and services meet stringent quality standards is essential to instilling trust and reliability among consumers and stakeholders. Quality Assurance (QA) and Quality Control (QC) are pivotal components of a robust Quality Management System (QMS), yet they serve distinct purposes, operate at different stages, and have unique objectives. This article delves into the differences and similarities between QA and QC within the context of the medical device industry.
What is Quality Assurance?
Quality Assurance (QA) is process-oriented. In the medical device industry it involves the systematic processes, procedures, and activities implemented to ensure that products meet predefined quality standards and regulatory requirements. QA focuses on prevention rather than reaction and it aims at minimizing defects and deviations throughout the entire product life-cycle, from design and development to manufacturing and distribution. It emphasizes compliance with regulations, adherence to standards, and the implementation of robust quality management systems. To put it simply: QA is about making sure you do the right things, the right way.
What is quality control?
Quality Control (QC) is more product-oriented. It's about verifying that the product meets the specified requirements and/or standards. This is typically something that is done at several stages during the production process. For example, inspection of raw materials, various in-process checks and final product testing. The goal of Quality Control is to identify and rectify defects or deviations in the finished product before it reaches the customer or end-user. This means that "QC is about making sure the results of what you've done are what you expected".
Why do we need quality control and quality assurance
As mentioned above, the goal of regulations is to ensure manufacturers bring safe and performant products to the market. The regulatory requirements encompass as well requirements related to the implementation of Quality Management Systems, including Quality Assurance and Quality Control.These are further explained in industry standards such as e.g. ISO 13485 and are part of best practices. By implementing proper QA and QC, you minimize the risks of regulatory sanctions or product recalls.
Further on the topic of safety, the end-users of the product are central. By implementing appropriate QA and QC, it helps safeguard the safety of patients and other end-users and enhances customer satisfaction
Risk Management and risk control are central in the development of medical devices Implementing appropriate QA and QC activities are part of controlling risks on two fronts, both in a preventive way (QA) as in a reactive way (QC). By making sure the proper processes are in place and well implemented and having checkpoints to verify produced devices meet the set requirements, reduces the risk of liability and potentially financial losses afterwards.
QA and QC both are part of the Quality Management System. They are part of the bigger picture of continuous improvement to reduce risks and increase efficiency.
Top 5 main differences between QA and QC
1. Proactive (QA) vs. Reactive (QC)
QA focuses on preventing defects by establishing and implementing robust quality management systems and processes, whereas QC involves detecting and correcting defects after they occur.
2. Process (QA) vs. Product (QC)
QA is concerned with ensuring the effectiveness of processes and systems, while QC evaluates the quality of finished products.
3. System (QA) vs. Parts (QC)
QA focuses on the processes, policies, procedures and documentation that is part of the full Quality Management System. QC on the other hand is focused on examining specific components or units of the product.
4. Creation (QA) vs. Verification (QC)
QA defines the framework for quality within an organization, while QC is part of verification. It verifies compliance with the requirements of the quality framework by testing and inspection. This also shows that QA starts earlier on the timeline than QC.
5. Entire Team (QA) vs. Dedicated Personnel (QC)
Even though most companies have a dedicated person or team that is focused on making sure the Quality Management System is performing well, QA affects the entire organization. Every member of the company needs to contribute to the quality improvement efforts. QC typically involves dedicated trained personnel that is responsible for specific inspection and testing activities.
Similarities between QA and QC
1. Adherence to Policies, Procedures, and Methodologies
The Quality Management System defines the quality related policies, procedures and methodologies within an organization. Both QA as well as QC are part of the organization and operate within the Quality Management System. Therefore both are guided by those policies, procedures and methodologies to ensure consistency and compliance.
2. Ensuring High-Quality Product Standards
One of the key focus points within the Quality Management System are customer focus and regulatory compliance. The whole system is built to allow the organization to work in a consistent and compliant way and to achieve those goals. Both QA as well as QC are part of these efforts, aiming to maintain high-quality product standards and specifications that meet the customer and regulatory requirements.
3. Proactive Issue Prevention
Even though QA is process-oriented and QC is product-oriented, both are aiming to ensure that the final product that is brought on the market is safe, performant and meets the specified requirements. When potential quality issues are being identified and addressed proactively through QA and QC activities, it minimizes the risks of defects, deviations or regulatory issues afterwards.
4. Commitment to Continuous Improvement
QA and QC both fit into the plan-do-check-act approach of the Quality Management System. They both emphasize the importance of continuous improvement, allowing to find and implement opportunities to improve processes, products and systems over time.
The Role of QMS in Quality Assurance and Quality Control
As mentioned before, the Quality Management System serves as the backbone for QA and QC. The QMS encompasses, the policies, procedures, documentation and resources that are required for implementing effective and compliant quality management practices. The QMS provides the overall framework, which allows to define the quality policy, quality objectives, adopting a risk-based approach and ensuring compliance with regulatory requirements. QA and QC processes are fully integrated in the QMS and help achieving consistent product quality, compliance and customer satisfaction.
Both ISO 13485 as well as ISO 9001 are internationally recognized quality management system standards and both emphasize the importance of QA and QC activities.
ISO 9001 sets forth requirements for a quality management system applicable to all industries, focusing on customer satisfaction, continual improvement, and the prevention of nonconformities. It emphasizes the need for organizations to establish and maintain effective QA and QC procedures to ensure product quality and meet customer expectations.
ISO 13485 specifically targets the medical device industry and outlines requirements for a quality management system that demonstrates the ability to provide medical devices and related services that consistently meet customer and regulatory requirements. It places a strong emphasis on risk management, process validation, and product traceability, all of which are integral components of QA and QC activities.
By adhering to the principles and requirements outlined in ISO 9001 and ISO 13485, organizations can establish robust QA and QC frameworks that not only facilitate compliance with regulatory standards but also enhance operational efficiency, mitigate risks, and drive continuous improvement initiatives.
In essence, the successful integration of QA and QC processes within a comprehensive Quality Management System (QMS) not only ensures product quality and regulatory compliance but also positions organizations to pass audits and achieve success in the competitive medical device marketplace.
If you'd like to learn more about how Matrix can help you establishing and implementing compliant QA and QC processes, don't hesitate to book a demo!