NEU!! Entwickelt SxMDs mit einem strukturierten eQMS, einschließlich auditfähriger SxMD-Vorlagen, die an EU- und US-Standards angepasst sind. Mehr Erfahren!
What is a Device History Record (DHR)?
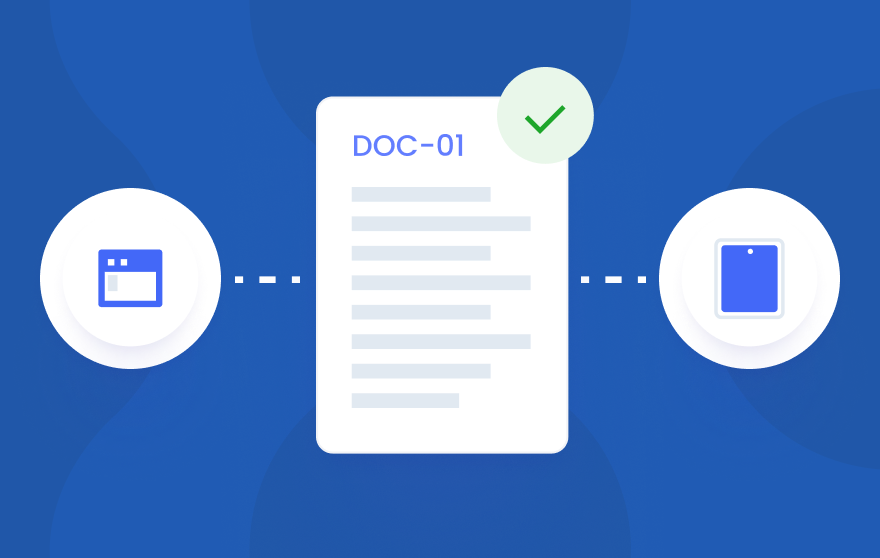
Each medical device has a unique journey, intricately documented in its Device History Record (DHR). The DHR highlights the design documentation to completely document the product realization process for any medical device.
In the scope of medical device regulation the Design History File (DHF) will show the journey of the device's design, the DHR gives insight into the manufacturing procedures and circumstances.
As regulators scrutinize production processes, the DHR provides clear evidence of compliance and adherence to quality standards.
The FDA has defined what they expect from a Device History Record.
Defining Device History Record (DHR)
A Device History Record encapsulates the manufacturing narrative of a medical device, archiving every critical step.
In its essence, a DHR is a compilation that meticulously chronicles the production lineage—from raw materials to finished product—serving as indisputable proof of a device's compliant creation.
This regulatory dossier furnishes the bedrock for product integrity and post-market scrutiny, embodying the manufacturing process's transparency.
DHR's Role in Manufacturing
The DHR ensures adherence to production protocols, and conformance with the Device Master Record (DMR) throughout the manufacturing process.
"Accurate DHRs are pivotal for maintaining product quality and enabling traceability in medical device manufacturing."
It is a critical tool for verifying that each manufactured batch meets the predefined criteria, ensuring consistency, safety, and regulatory compliance of produced devices.
A well-maintained DHR supports efficient traceability in post-market activities, including potential recalls, thus safeguarding both the manufacturer's reputation and patient safety.
Regulatory Compliance
The FDA has defined the requirements for Device History Records (DHRs) in 21 CFR Part 820.184. According to these regulations, each manufacturer is required to maintain DHRs for each batch, lot, or unit to demonstrate that the device is manufactured in accordance with the Device Master Record (DMR) and the requirements of this part. The DHR should include or refer to the following information:
(a) The dates of manufacture;
(b) The quantity manufactured;
(c) The quantity released for distribution;
(d) The acceptance records that demonstrate the device is manufactured in accordance with the DMR;
(e) The primary identification label and labeling used for each production unit; and
(f) Any unique device identifier (UDI) or universal product code (UPC), and any other device identification(s) and control number(s) used.
These regulations ensure that the DHR serves as a comprehensive record of the device's journey, providing evidence of compliance and adherence to quality standards during the manufacturing process.
Inclusivity of detail in DHRs ensures regulatory bodies can verify compliance without ambiguity.
Precision in maintaining DHRs mitigates the risk of non-compliance, which can carry significant financial and reputational repercussions.
Importance of a detailled and well maintained DHR
The integrity of a DHR directly correlates to the caliber of patient safety measures. Precision-engineered medical devices require equally meticulous DHRs to assure consistent quality standards.
A comprehensive DHR serves as a foundational element of a robust quality management system (QMS), setting the stage for sustainable compliance and operational excellence. Each device's journey from raw materials to patient use needs to be documented detailled enough to create a trail for investigating deviations or non-conformances that arise post-distribution to enhance accountability and patient safety.
In essence, the robustness of a DHR is synonymous with a company's commitment to uphold quality and safety standards.
The DHR should serve these main goals:
Documented Proof of Conformity: DHRs provide evidence that devices are manufactured according to regulatory standards and DMR specifications.
Traceability and Accountability: Each device's history is recorded in detail, allowing the tracing of any non-conformity back to its origin.
Facilitation of Audits: Maintaining DHRs assists in providing straightforward answers during inspections and audits, showcasing a culture of compliance.
Readiness for Regulatory Inquiries: DHRs must be retrievable and comprehensively detailed to respond promptly to any regulatory inquiries or actions.
The DHR's records of lot and batch numbers, manufacturing dates, and test results promote a culture of transparency. In scenarios where deficiencies manifest, these records facilitate quick identification of affected units, empowering manufacturers to swiftly isolate and resolve the issue while maintaining rigorous adherence to quality standards and regulatory expectations.
Constructing a Compliant DHR
A compliant Device History Record (DHR) embodies meticulous documentation and precision, representing more than a mere procedural formality—it stands as the quintessence of manufacturing diligence. Ensuring that every DHR entry rigorously aligns with the corresponding Device Master Record (DMR), it verifies that each device batch meets the requisite specifications and regulatory mandates. These records underscore the reliance on standardized processes, incorporating comprehensive details such as manufacturing dates, quantities produced and distributed, acceptance testing results, and the associated labeling and unique identification codes. By faithfully encapsulating this information within the DHR, manufacturers not only conform to 21 CFR Part 820.184 but also fortify their commitment to excellence in device quality and patient safety.
Without a basic DHR that describes the manufacturing of the first devices which were to be used for performance validation, a successfull FDA registration for market access is hardly possible.
Essential Elements to Include
Manufacturing dates must be meticulously recorded.
Each DHR should carefully detail the quantity of devices manufactured, ensuring accuracy for later reference. Tracking the volume of devices not only serves compliance requirements, but it also provides critical data for production planning and market supply estimations. Moreover, precision in recording quantities is foundational to maintaining the integrity of inventory controls and reconciling production outputs with distribution records.
Quantities released for distribution are pivotal.
Careful annotation of acceptance records is paramount. These documents serve as a testament to the device's compliance with its DMR, offering a clear link between what was intended in the design and manufacturing phases to what is realized in the final product. Without such records, a manufacturer's quality assurance process remains incomplete and potentially non-compliant.
Labeling and unique device identifiers are essential.
Documentation and Record Maintenance
Accurate documentation ensures compliance with regulatory standards, serving as an evidentiary cornerstone for audits and inspections. Maintaining precise records equates to a robust quality assurance framework that reinforces trust in the medical device industry.
Record integrity must be preserved unfailingly. A meticulous approach to documentation is not merely a regulatory formality; it is the linchpin of product traceability and accountability. Without uncompromising attention to detail in record-keeping, the reliability of the entire medical device lifecycle is compromised.
Therefore, comprehensive documentation requires strict adherence to established procedures. This is not an area for shortcuts; thoroughness in maintaining DHRs guarantees that devices meet both legal and safety standards.
Central to DHR maintenance is the ability to demonstrate manufacturing consistency. The DHR must reflect adherence to the DMR, thereby ensuring each device batch upholds the pre-defined quality benchmarks and specifications.
Finally, the preservation of DHRs is critical for long-term accountability. Records must not only be thorough at the moment of creation but must be maintained to withstand the tests of time, safeguarding against future liability concerns.
The DHR's Function within QMS
Within the Quality Management System (QMS), the DHR serves as a critical tool for continuous monitoring and improvement. It provides tangible evidence of conformance with established processes, acting as both a checkpoint for quality assurance and a foundation for evaluating the efficacy of manufacturing protocols.
The DHR's thorough archival of production details augments the traceability and accountability of the QMS framework. It enables a connection between a product's lifecycle stages, ensuring all compliance aspects are documented in detail and with traceable information. Such documentation is paramount when a product's quality is under scrutiny or when pinpoint, corrective actions are necessary to maintain adherence to regulatory benchmarks or customer complaints.
Enhancing CAPA Investigations
Corrective and Preventive Action (CAPA) investigations gain from rigorous DHRs.
By triangulating issues through DHR insights, CAPA teams expedite root cause analysis. Capturing manufacturing nuances in DHRs aids in swiftly pinpointing discrepancies, facilitating efficient and accurate CAPA responses. A comprehensive DHR illuminates patterns over time, spotlighting systemic issues faster.
A DHR can streamline CAPA process execution. You can take a look here at our latest video on CAPAs and the zoom in on the CAPA effectiveness check and Root Cause Analysis.
When CAPA trails lead to manufacturing processes, DHRs stand as invaluable. They contain granular detail – from production timelines to test outcomes – pivotal for CAPA investigators seeking to pinpoint the genesis of an issue.
DHRs support focused issue resolution and regulatory compliance, relying also on detailled information of the product's specifications and the potential risks from the manufacturing procedures in the Design History File (DHF).
Advancing Process Improvements
DHR data inform strategic enhancements in manufacturing processes. Client feedback tied to specific batches offers invaluable insights into process refinement opportunities.
Through meticulous record-keeping, DHRs surface trends that isolate manufacturing anomalies, enabling adjustments to enhance product quality. Leveraging precise historical data, decisions become data-driven, leading to more effective process modifications.
Advanced DHR analytics predict potential quality issues, allowing preemptive process adjustments before defects arise. This predictive approach to quality management reduces wastage and refines manufacturing efficacy, marking a substantial stride in process improvement.
By comparing DHRs against predetermined quality benchmarks, companies can continuously elevate their manufacturing standards. This iterative refinement ensures that each product iteration benefits from the learnings of its predecessors.
DHRs act as a catalyst for continuous improvement in production lines. They are a critical tool for sustaining a competitive edge through constant process optimization.
Use Matrix Requirements to leverage DHR information
In the MatrixRequirements ALM and QMS platform, the integration of DHR information provides numerous benefits for Quality Management (QM) responsible persons in device manufacturing companies. By utilizing aspects such as traceability between production test results, risk management, product design and quality management procedures, non-conformity information, and documentation of production, QM responsible persons can achieve proof of product conformity for quality assurance and reliability substantiation.
One of the key advantages of using MatrixRequirements is its item-based approach to documentation. This approach allows for the creation and management of individual information items, such as test results, risk assessments, and design specifications, which can be linked and traced throughout the product lifecycle. This level of traceability ensures that all relevant information is easily accessible and can be reviewed for compliance and quality control purposes.
Furthermore, the MatrixRequirements platform provides a unified solution for both quality management and product documentation. This integration eliminates the need for separate systems and allows for seamless collaboration between different teams and departments. By having all documentation in one place, QM responsible persons can streamline their processes and ensure that all stakeholders have access to the most up-to-date information.
Digitalization plays a crucial role in leveraging DHR information effectively. With MatrixRequirements, QM responsible persons can take advantage of automated versioning of information items, ensuring that changes and updates are properly tracked and documented. This not only improves the accuracy and reliability of the information but also simplifies the audit trail and facilitates compliance with regulatory requirements.
In conclusion, by leveraging DHR information in the MatrixRequirements ALM and QMS platform, QM responsible persons in device manufacturing companies can optimize their processes, enhance traceability, and ensure compliance with regulatory standards. The item-based approach to documentation, unified platform for quality management and product documentation, and the use of digitalization with automated versioning all contribute to the efficient use of information from production and product/batch test reports.